Electric Vehicles (EVs)
EVs and Rare Earth Mining
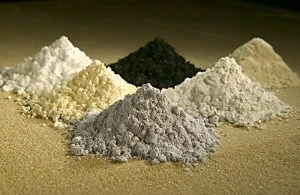
Rare earth metals.
Where are all the earth’s rare metals mined? Are electric vehicles (EVs) really so environmentally sound and friendly?
Rare earths are difficult to find and obtain in most parts of the world, and they are used a lot in all sorts of common and accessible products like mobile phones, cars, aeroplanes, missiles, radars etc. Rare earths are also abundantly used in EVs. EVs use special magnets to power their engines, and most of the magnets in EVs that can cover longer distances on one battery charge are made from rare earth metals. The metals aren’t necessarily rare, but they can be dirty and difficult to process. Many of the processes related to rare earth extraction (getting the rare earths out of the ground) are dangerous, environmentally unfriendly, and, in many cases, the mining workers are older boys and younger men. The process to obtain many of the rare earths is environmentally destructive and produces radioactive waste.
Of the 17 rare earths, neodymium is possibly the most needed rare earth in the world right now. EVs cannot function without neodymium, and lithium – which is currently mostly found in Bolivia.
China has a large portion of the rare earth mining pie and supply network. Back in 2010, China produced as much as 90% of the rare earths that the world needed, and it now seems obvious to me why China’s economy and infrastructure was booming so much at the time. Also, around this time, the rest of the world started to see just how China ruled the rare earth market and power struggles commenced.
Without the rare earth metal, neodymium, an iPhone cannot vibrate and wind turbines would not work. In order for EVs to gain more milage between charges, Rare Earth Permanent Magnets (REPM), which use neodymium, are required. REPMs are the most powerful magnets currently available.
So, though rare-earth elements are used in trace amounts, their unique properties, which include magnetic, heat-resistant, and phosphorescent qualities, make them essential in the production of products like batteries, car engines, EVs and LCD TV displays. EV motors, iPhones, military jet engines, batteries, and even satellites all have something in common: They require rare-earth elements to function.
Other elements like terbium, tritium and europium are crucial to targeting mechanisms in all high-tech weaponry systems. The higher-tech that an EV becomes, a corresponding increase in the level of rare earth mining will be required. The more EVs that are run on the roads (resulting from strict emission standards and government taxing), the more the rare earth resources will be called upon to build and maintain the EV fleet. Currently, an EV battery doesn’t last much longer than 10 years, so EV battery replacement requirements will mean that much more rare earth metals will be needed to maintain the ever-growing global EV fleet.
As of 2018, China had 37% of the world’s rare earth deposits. Brazil currently has 22%, Vietnam 18%, Russia 10% and India has 5.8%. The rest of the world, including the US and Japan, have the rest.
Despite having more rare earth ore than the US, India only mined 3,000 tonnes of rare earths in 2020. During 2020, the US mined 38,000 tonnes. Meanwhile, Australia mined 17,000 tonnes and China mined 140,000 tonnes. In 2020, the US had 16% of the production rate of the world’s rare earths; Australia had 7%, and India had 1%.
In 2020, the following countries were the biggest producers of rare earth metals:
China, mine production: 140,000 MT
United States, mine production: 38,000 MT. The US is also a major importer of rare earth materials, with their demand for compounds and metals worth US$110 million in 2020. The US has classified rare earths as critical minerals, and it is a distinction that has come about from recent trade issues between the US and China.
Myanmar (also known as Burma), mine production: 30,000 MT. Myanmar mined 30,000 MT of rare earths in 2020, up from 22,000 MT the previous year. Myanmar provided 50% of China’s medium to heavy rare earths feedstock.
Australia, mine production: 17,000 MT. Australia holds the sixth largest-known rare earths reserves in the world. It is poised to increase its output, where the production of neodymium-praseodymium products is projected to increase to 10,500 tonnes per year by 2025. Northern Minerals opened Australia’s first heavy rare earths mine in 2018. Its main products are terbium and dysprosium, the latter of which is used in technology for things like permanent magnets.
Madagascar, mine production: 8,000 MT.
India, mine production: 3,000 MT. India holds almost 35% of the world’s total beach sand mineral deposits.
Russia, mine production: 2,700 MT. Russia intends to increase the nation’s share of global rare earths production from the current 1.3% level to 10% by 2030.
Thailand, mine production: 2,000 MT.
Vietnam, mine production: 1,000 MT.
Brazil, mine production: 1,000 MT.
Rare-earths are also mined in South Africa, Canada, Estonia, and Malaysia.
Is an internal combustion engine’s resultant emissions and fossil fuel use really worse than the rare earth metal production mining for EVs and other high-tech electronics? I would question whether a modern and new internal combustion engine with its catalytic converter to capture any emissions is worse than an EV’s definite connection to negative environmental impact and questionable work-force ethics.
Sometimes it is easier to disregard these pre-showroom EV facts and talk about the post-showroom EVs being so wonderful and environmentally-friendly with their so-called zero emissions. Perhaps hydrogen-fuelled cars (to a certain extent), solar energy, and, definitely, cars running on biofuels are a sounder transport investment, but I guess money, power and business links still talk louder for some.
EV Revolution
Let’s ditch fossil fuels and crude oil for a while, since some say that oil is considered environmentally unclean and unfit for burning. So, what about electric? Which of our earth’s finite resources are needed to make electric vehicles (EVs)? It will be Tanzania, Venezuela, the Democratic Republic of Congo, Canada or even Brazil who could be the providing the rest of the world with precious raw metals that the greener EV requires.
As electric cars appear to be going mainstream and all our main automotive manufactures look to ditch internal combustion engines (ICEs) by 2025-ish, these big automotive giants have to source and make investments into electric cars and their necessary componentry. Countries like South Africa, Tanzania, China and even Australia have very mineral-rich and rare metal resources. These countries and their mining industries are the world’s best environmentally friendly strategy to power EVs and their mass production.
There is a global race on that is driving the demand for countries, including quite a few in Africa, to mine as much of their precious metal resources to equip the world with a greener fleet of vehicles. This clambering for sourcing all the right stuff for EV production en masse could soon provide billions of dollars into certain countries’ GDP rates.
Rare metals like copper, lithium, cobalt and nickel are some of the most discussed metals in EV production demands. Other metals like neodymium (a rare earth metal), aluminium and zinc have emerged as some other new resources that will be needed in the rapid quest for a greener world. Statista, a German company specializing in market and consumer data, estimates that the demand for metals such as nickel, aluminium, and iron (all the critical components in EVs) will jump to as much as 14 times the rate that it is now by 2030. This huge demand for environmentally friendly EV minerals for meeting the green EV car revolution will provide a great cash injection for a well-endowed African state. Demand for metals like lithium and graphite are also expected to rise substantially, even by as much as 9-10 times by 2030.
The large estimated increase (14x) in demand for the clean EV minerals to meet the intended global EV production rates over the next ten years is accompanied by the need for vehicle battery outputs and infrastructure, which are expected to rise by millions of times over in the very near future. Even Toyota recently announced a 13.6 billion US investment into electric cars and hybrids, with some 9 billion US dollars to be spent on battery production alone. This is fantastic news for the environment and carbon zero.
The increase in demand for these rare and hard to obtain metals is pushing top mining and big investment companies around the globe to invest in the acquisition of key materials used in the production of EV batteries, EVs themselves, and their much needed electrical infrastructure. Solar energy componentry, as well as the EV requirements, all point towards an enormous boom in demand for these rare and hard to reach resources, as well as creating an opportunity to make even more money than the awful and “dirty” fossil fuel endeavours.
It is expected that the sales and production of EVs will continue to accelerate quickly over the next five years. Big automotive giants who are changing to larger-scale EV production have major mining countries like South Africa, Namibia, the Democratic Republic of Congo (DRC), Tanzania, Zimbabwe and Botswana on their radar. These are just some of the main African countries, let alone other countries around the world, who enjoy bountiful reserves of some of the world’s most precious metals and minerals: minerals such as gold, diamond, cobalt, iron ore, coal, and copper. Meeting the demands by governing authorities and their growing appetite for better and greener EVs will be much better for the environment – and for special places like Africa, I’m sure.
President Hakainde Hichilema is the new president for Zambia, and he has recently announced plans to ramp up mining in particular, and to jump-start Zambia’s economy. Part of his economic plan provides for the rapidly growing EV battery industry, with cobalt and copper identified as key components. The workforce will be a great place for young men from the age of 15 years old, who will be able to work in the dangerous mining industry. Countries like Zambia and Tanzania are working hard to supply the developed countries of the world with the rare metals. The developed countries are considered to have a higher status and economic standing, a better understanding of the environment, human ethics, health and emission standards. Their demand for a green EV world is a good thing for all people and the environment.
As the big green machine, Tesla, and auto giant Toyota are joined by other larger EV-producing manufacturers, African mining countries are going to have to move faster than ever to meet the demand put on them by the governing authorities of the world and their ever-increasing and severe carbon emission goals and standards. The president of Zambia, Mr. Hichilema, has wasted no time in announcing his administration’s hopes to quickly provide the clean EV battery supply chain and invest much of his country’s proceeds into its development.
Rare metals and their difficult and extensive underground extraction methods are needed in EV lithium ion battery technology and are critical for improving the driving range of electric vehicles so that they can compete with the best, most frugal, “archaic” ICE technology and emission-capturing methods. These rare metals are buried beneath the fields of African nations, ready to be harvested by economically sound, rich and developed countries with zero carbon emission goals and standards.
South Africa, a mining giant, has also announced plans to set up production plants to manufacture EVs of their own, including plants for the manufacture of EV components, such as EV batteries. This could see South Africa as one of the multi-billion-dollar raw material producers of the world. South Africa already has its raw material extraction industry, its capital markets, and its existing manufacturing and export infrastructure to build upon.
Environmentally friendly keywords that current governments, economists and greenies around the world are sharing with the public are words like carbon emissions, climate change, EVs, EV infrastructure, mining, metals, zero carbon, clean technology, investment and climate crisis. All of these keywords correspond with the rising demand for the precious metals used in EV production.
As it stood in 2020, the total global nickel reserves amounted to approximately 94 million metric tons. Of that amount, it was Indonesia that held the world’s largest share. Following the tropical and beautiful Indonesia is Australia, with our nickel reserves estimated to be 20 million metric tons. Best we get stuck in, then!
ICE to EV Conversions
Converting your favourite drive over to electricity seems like a reasonable alternative to buying a brand new EV with a massive price ticket now, doesn’t it? Flicking through the list of brand new EVs that you can currently buy in Australia soon has you eyeing up figures of well over $50 k. At the moment, the cheapest EV in Australia is the MG ZS EV with its $45k price tag. A bog standard Nissan LEAF comes with a drive away price of around $54k. How about a Tesla? Anywhere from $65–93k will get you into a Model 3. Converting an older classic car to full battery-electric power has coolness written all over it. The end result might even gain you a Greta Thunberg award!
Is it possible? Can we convert a favourite oil burner to electric power? If I was to convert my drive to EV, it would have to be a conversion of a favourite car – something like an old Falcon or Commodore. Bringing one of these ideal cruisers up to EV spec would be a challenge, but a challenge with great satisfaction. Installing an electric drivetrain into an old vehicle could help keep some classics on the road and out of the scrapyard. Why not take the restoration, recycling and retrofitting to the next level and repower classic cars?
There have already been a few conversions of this sort of thing in certain areas around the globe, usually in someone’s garage late at night, where the candle burns bright and long into the night. Considering performance enhancements alone, a good off-the-shelf electric drive system will almost always be a substantial performance upgrade for an old daily driver. Even some of the muscle car straight six or V8 powerplants are humbled by a rather conventional EV motor with its instant torque availability.
Converting a petrol or diesel car into an electric one means replacing its combustion engine and fuel system with an electric motor coupled with a traction battery. Although the procedure looks relatively straightforward at first glance, it does mean that you do need to apply sound physics and DIY know-how on electrics to get yourself a car that moves in the right direction safely. There is some pretty high voltage happening beneath the skin of your old, converted classic that enables it to whistle up to 100 km/h in seven seconds, or less. Conversions are a substantial cost and do require appropriate re-certification tickets. However, the whole ordeal should cost quite a lot less than a new EV, at least by a few thousand when compared to a Tesla.
Things to work through.
Installing an electric motor into a gas or diesel car’s chassis and platform requires the skill to build up a drive train and axle to get the power from the electric motor out onto the road. The old gearbox that was essential to the old internal combustion engine (ICE) design is a useless mechanism for the new electric motor. The old gearbox has to go, and a new drive mechanism has to be designed and implemented.
The weight of the vehicle and the dimensions of the wheels directly impact on the choice of brakes and suspension. Not always but, more often than not, the car with a heavy battery pack will weigh more than the original set up. In order to function safely with the added weight and/or changes in weight distribution, the converted car must have some structural strengthening, brake and suspension upgrades and some modifications done in order to ensure that the changes marry up into a harmonious mode of EV transportation and driving pleasure.
The battery pack isn’t going to be cheap. You’ll easily spend in excess of $10–15k for a lithium-ion battery pack that is able to offer a respectable range over 100 km. Lead-acid batteries, like those used in golf carts, can often be installed, though they typically deliver a rather small operating range on one charge. Lithium cells are smaller and lighter, and can enable longer ranges, but they’re more expensive. How many batteries you’ll require will depend on the vehicle you’ve chosen and the space available in which to have them fitted. The new battery pack, as mentioned above, is very heavy and has to be carefully installed inside the car’s framework in a way that won’t compromise occupant space and safety, as well as ensuring excellent on-road behaviour.
One other small thing to think about is how you will heat or cool the cabin. ICE vehicles used the heat that comes from the engine design, but EVs need to run a different set up.
EV enthusiasts usually favour smaller and lighter vehicles for conversion, though the size of your wallet will also control what you can and can’t afford.
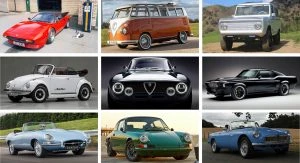
ICE to EV Conversions
Popular choices of cars that have been converted have been cars like the Honda Civic, VW Beetles, the Fiat 124 Spider, the Triumph Spitfire and MGs of the same era, Mazda Miatas or MX-5s, Toyota MR2s, and various Porsches. Pickup trucks and utes are also easy converters because they already have a big tray out the back to accommodate heavy batteries.
Mat Coates from Nelson, NZ, saw the potential of electric cars as a youngster who messed around with remote-controlled vehicles at age 10. His first conversion was a Mitsubishi GTO, so there’s an inspiration for you. How hard can it really be? All things considered, where there’s a will there’s a way. As long as you tick all the boxes and do the job right first time and do it well. A quiet classic that has been converted to EV propulsion is hard to beat and a rather special way of getting around.
A good place to start might also be to talk to the people at https://www.evolutionaustralia.com.au. These people already have experience in converting ICE vehicles over to being an EV.
Hyundai and Hydrogen
I’m showing my age a bit when I say that I can remember some of the earlier Hyundai cars – the Hyundai Pony and Hyundai Excel come to mind. Back in the 80s and early 90s, Hyundai cars were light, comfortable, and not really up to the same safety standards as the cars that were produced in other parts of the world. Nowadays, however, the story is completely different, and the South Korean automaker often tops crash safety tests with their vehicles, the vehicles are still comfortable, and the style and technology has won many awards. Hyundai has been always improving to the point where they are now a premium brand, very desirable, and leading the world on many fronts. Key new innovations from the Hyundai Motor Company (HMC) team are exciting and are part of Hyundai’s vision for building a cleaner, greener world that includes vehicles that no longer rely on fossil fuels.
Because of the past couple of years, where covid has taken the world’s centre stage, there has been a big shortage of semiconductors in the auto industry, to the point that some auto manufacturers have had to shut down. Semiconductors are used in the manufacture of electronic devices, including diodes, transistors, and integrated circuits. These devices have a wide application in anything electronic, including laptops, computers, appliances, and, of course, the modern automobile.
Like all vehicle manufacturers, HMC has been affected by the shortage and have had to temporarily suspend some of their factories. Despite the shortage, however, along with Toyota and Tesla, Hyundai is among a handful of automakers that actually increased their global sales despite the chip shortage.
However, Hyundai now plans to develop and build its own semiconductors so that they are not so reliant on chipmakers from other corners of the globe. Hyundai wants to make sure it has a steady supply of semiconductors for their projects on-and-into the future by making its own. It will be the parts and service arm for Hyundai, Kia and Genesis who would play a key role in the in-house development. Stockpiling the electronic chips would be important for Hyundai, so that when other global crisis occur, they will then be in a better position to weather the storm. Toyota and Tesla have already had stockpile contingency plans in place for some time, which has ensured that they fared well during covid.
Hyundai and Hydrogen
Hyundai are part of the Hydrogen Heavy Duty Vehicle Industry Group – comprised of hydrogen industry leaders Air Liquide, Hyundai, Nel Hydrogen, Nikola Corporation, Shell and Toyota. This Group has signed agreements with Tatsuno Corporation and Transfer Oil S.p.A. to industrialize globally-standard 70 MPa hydrogen heavy-duty vehicle high-flow (H70HF) fuelling hardware componentry. But, also, in Incheon, which is just west of Seoul, and in Ulsan, production plants will begin producing the hardware in the 2nd half of 2023 with an annual capacity of 100,000 hydrogen fuel cell systems.
South Korea’s influence on core Hydrogen components will see it as the world’s largest fuel cell production capacity, which will also help the HMC to diversify their business and tap into construction machinery and logistics equipment.
EVs might be the big talking point for some, but it is hydrogen that is the dark horse in the clean-green race. These two new fuel cell plants in Korea will accelerate the hydrogen economy and secure broader global market dominance. I reckon that Australia could be a hub for Hydrogen in the Pacific, don’t you think?
Hyundai’s wide-ranging hydrogen revolution accelerates with the showing of their 500 kW Vision FK sports car prototype and the e-Bogie autonomous commercial transport vehicles. HMG recently announced that it will launch next-generation hydrogen fuel-cell power units in 2023 that will double the power output, halve the cost, and reduce package size by 30%, when compared to current systems. Hyundai has a plan to offer “hydrogen for all” by 2040.
Hyundai’s Hydrogen Timeframe
In case you were not already aware, HMG is the parent of Hyundai, Kia and Genesis. By 2028, HMG says it will have applied fuel-cell systems to all of its heavy commercial vehicle models, including large trucks, significantly reducing transport-related CO2 emissions.
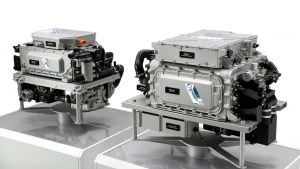
Hydrogen Fuel Cells
By 2030, Fuel-Cell Electric Vehicles (FCEV) will have achieved price parity with Battery Electric Vehicles (BEV), HMG says. And by 2040, HMG expects hydrogen to be available for everyone, for all vehicle types, and globally, triggering a lifestyle revolution.
Models for the Future
The Vision FK sports car is a 500 kW, hydrogen-powered high-performance prototype coupe that is capable of accelerating from 0-100 km/h in less than 4 seconds, while still offering a range of 600 km between top ups. The Vision FK’s fuel cell unit carries N Performance branding, suggesting that it would be a future Hyundai N model rather than a luxury-focused Genesis. HMG’s head of R&D, Albert Biermann, would not be drawn on when the Vision FK would go from prototype to production, but he did confirm that the next-generation Nexo fuel-cell SUV will launch “in the second half of 2023 followed by a Staria” The Staria is a people mover recently launched in Australia. “We are also working, of course, on fuel-cell cars for Kia and Genesis. That will take a little longer time. After 2025 you can expect further fuel cell applications.”
The e-Bogie commercial application is a fuel-cell-powered autonomous trailer that could revolutionise commercial transportation. Biermann also stated, “We are working full throttle on commercial [first] because that is the most effective way to avoid CO2. We are putting a lot of focus on fuel cells, not only for passenger cars but also for commercial vehicles.”
HMG’s Chairman, Euisun Chung, is even more emphatic about the significance of hydrogen fuel cell applications toward a sustainable future. “This may be the last train to a Hydrogen Society, and time is running out. Hydrogen is the most powerful and pragmatic solution to overcoming environmental challenges. Hydrogen mobility will accelerate human progress.”
He went on to say that Australia may have a role to play. “We know Australia is a country with vast and abundant renewable energy. We are exploring business opportunities in Australia with our partners. Our goal is to build a sustainable ecosystem for [a] global hydrogen society.”
He also said that, “We will not immediately phase out internal combustion engines (ICE) commercial vehicles, but we are not starting any new developments of ICE. No new models and no new platforms. Everything will go forward with BEVs and FCEVs.”
Interestingly, according to Hyundai’s head of fuel cell development, Mr Saehoon Kim, FCEV technology has one huge advantage over BEVs: “The main problem with [a] BEV is the scalability of batteries. For a small EV it’s okay, but for commercial large scale [operation] the question immediately is …. How are we going to stack all these batteries with the heavy weight, and who is going to be happy with the low range? So, in this case fuel cell fits perfectly.”
Hyundai’s heavy commercial fuel cell program is already well advanced. In mid-2020, 45 Hyundai Xcient fuel cell trucks began commercial operation in Switzerland. Biermann stated that the trucks covered 210,000 kilometres per month and have saved 130 tonnes of CO2 emissions every month in operation.
The key to Hyundai’s commercial strategy is its third-generation fuel-cell system, which is in the final stages of development. Hyundai expects to launch two units in 2023, one producing 100 kW for passenger vehicles and SUVs (including the next Nexo and Staria FCEVs), and a 200 kW unit for commercial applications. It has been said that by using two fuel-cell systems for trucks Hyundai can provide around 350 kW, which is equivalent to the power of current diesel engines used in trucking logistics.
This is all very exciting news and one that I have welcomed hearing. I’m a fan of the new hydrogen fuel-celled vehicle technology moving forward. This is Hyundai at its best, and we can only continue to watch this space.
Current Hyundai achievements:
The current ICE Hyundai i20 N has been crowned champion of Top Gear’s Speed Week. The 26 fastest cars in the world participated in Top Gear’s Speed Week 2021. It was the Hyundai· i20 N’s sharp handling and everyday usability that stood out to those in the Top Gear team.
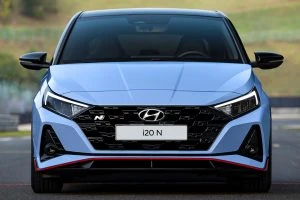
Hyundai i20N